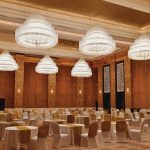
Lighting Controls Solution for Hospitality Industry: The Leela Palace, Gandhinagar, Gujarat
May 6, 2024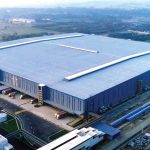
Evio’s one of the Land Mark Project. Flipkart Big Box Haringhata (Kolkata) warehouse
May 6, 2024Industry Brief
The internet of things (IoT) as we already know, is a giant network of connected things and people. This seemingly endless web of interconnected devices is said to be the pinnacle of technological advancement. From ordering an Uber to efficient elevator alignment to maximizing energy efficiency, there is literally no limit to the potential physical accomplishments of the IoT. The interesting fact is, we are still around the peripheries of the full accomplishment of the IoT. Of all the fields in which the Internet of Things is set to disrupt norms, the field of electricity is perhaps the most impacted thus far. General Electric (GE) predicts that $1.3 trillion of value can be captured in the electricity value chain from 2016 to 2025 globally by IoT.
Since the discovery of electricity in the 1800s, there has been a global utilization to this energy source. In India alone 414.10 GWh of electricity were used in 2019. Industrial consumption represents 41.6% of this total electricity consumption.
Electrical energy powers almost everything in Industrial buildings, from water pumps to the entire production plant. As much as Industrial facilities rely on electricity for their daily operations, electrical energy comes with a serious caveat – Maintenance.
Electrical maintenance in Industrial facilities can be split into two major areas – Maintenance of energy generating equipment and maintenance of energy consuming devices.
Energy generating equipment or devices refers to those components which are used to manage and generate the electrical energy needs of an Industrial facility. A typical example will be a transformer. Transformers collect electrical energy from the grid and supply to the entire industrial facility. If a transformer were to get bad, the electricity supply in an Industrial facilities will be interrupted, if only momentarily at best. Another example of an energy generating equipment typical to industrial properties is the captive diesel generator.
All electricity generating equipment have life spans and limitations with respect to power input and output, as well as other environmental constraints. These limitations necessitate maintenance.
Energy consuming devices on the other hand are also commonly referred to as end devices. These are the equipment and devices responsible for electricity consumption in Industrial & Commercial facilities. They are found everywhere within the facilities, and are responsible for the day to day operations of industrial and commercial facilities. They include electric kettles, bulbs, conveyor belt, motors, pumps etc. They enhance occupants experience and contribute to the establishment with a competitive edge. Just like electrical energy generating equipment, the end user devices are also a constraint, hence the need for electrical maintenance.
Electrical maintenance covers all aspects of testing, monitoring, fixing and replacing elements of an electrical system. Though the possibilities of using IoT for electrical maintenance are endless, these possibilities will be looked at in line with the four major areas of electrical maintenance – Testing, Monitoring, Fixing and Replacing electrical systems.
How IoT can be used for Electrical Maintenance in Industrial Facilities
- Testing of electrical equipment
Testing of electrical equipment is important not only for the equipment being tested, but is also directly linked to the safety of all the occupants in an Industrial or commercial building. Industrial facilities electrical equipment have to be tested on a regular basis to ensure that the equipment’s are functioning properly and are in line with regulatory standards.
Before the advent of IoT, all forms of electrical appliance testing in industrial & commercial buildings was done manually, based on a schedule. The testing in itself followed standard procedures, such as shaking, smelling and running of the equipment to check for possible faults. The main problem with this form of testing was its heavy reliance on the principle of “If checked parts are OK, then the whole is OK”. This principle was not very effective, because it did not take in to consideration all the components of the Industrial facilities electrical appliance being tested, neither did it evaluate the impact of external environmental factors on the appliance.
With the implementation of IoT systems by Industrial & commercial facilities, this phase of electrical maintenance can be accomplished more effectively. This is achieved by linking up all the Industrial facility’s electrical equipment to the facilities IoT platform, into which analytics are incorporated. Based on the communication between the building’s electrical equipment and every other appliance in the facility, O&M teams will be able to act more efficiently. Leveraging IoT, thresholds could be set within which the system will automatically signal for management to ensure testing or repair. This increases efficiency, as management will not have to schedule for checks when they are not needed, while only getting results based on partial human analytics.
- Monitoring of Electrical Equipment
The monitoring of Industrial facilities electrical equipment implies a continuous and ongoing survey and collection of data with respect to the operations and functionality of the installed electrical system. The crucial nature of this task requires the provision of specific and accurate values on which management can forecast and plan. If these data are collected through human survey, there will always be a margin for error, which could cause management to make all the wrong decisions.
By leveraging the IoT platform, the management of facilities could have real time updates and accurate figures with regards to the performance of electrical equipment within a facility. With the monitoring of the Industrial facilities electrical equipment being done automatically and on a continuous bases, management can be furnished at any time with actual and concrete data on the performance of the different electrical appliance within the facility.
This data could further be accumulated along stated parameters to provide reports and projections with respect to the overall electrical needs of the facility. With IoT incorporation into electrical equipment, everyday electrical equipment transcend from stationary objects to smart devices which can influence the overall electrical maintenance pattern of the installed electrical ecosystem. IoT provides an assurance of constant monitoring and precise data collection for effective decision making.
Today businesses apply three techniques to achieve Peak Overall Equipment Efficiency (OEE) & Utilization to realize their IRR & ROI
- Fixing and replacing electrical equipment
This is the most commonly implemented phase of electrical maintenance. All electrical equipment, no matter how durable, are subject to breakdown. Breakdowns though inherent, if managed properly will not hinder the normal operations of a facility. Unfortunately, it is near impossible to properly manage electrical appliance breakdown relying on a 100% manual system. This is why IoT is the best possible method by which to manage electrical appliance breakdown and replacement.
By using IoT, Industrial facility operators are able to know beforehand (Predictive intelligence) whether or not electrical equipment will breakdown, and when specific electrical equipment will need replacing (Predictive Maintenance).
When electrical equipment in an Industrial facility are interconnected with other devices and linked up with an IoT platform with analytics, the sensors within the electrical equipment pick up valuable and time sensitive data which the human eye could miss. By correlating this data with that from other sensors within the installed electrical ecosystem, as well as liaising with external data sources such as those about the weather, Industrial facility managers can know with near certainty, the best time to inspect the electrical ecosystem, or schedule for repair, servicing or replacement.
Everything can therefore be planned carefully to avoid a breakdown in daily operations.
Conclusion
In conclusion, IoT is being used by various industries, sectors and for increased efficiency and maintenance. Electricity, being the major source of power in almost all sectors is using IoT to manage and maintain equipment and devices that both generate or receive electricity. Some of the most common uses of IoT in electrical maintenance are testing, monitoring and fixing and replacement of electrical equipment.
Below is a snap shot of the solutions and benefits which evio things electrical ecosystem IOT brings to the table. As more and more industry sectors are adopting IoT for electrical maintenance, it is important that you take a look at your facilities and ensure that you are adopting this latest technology in order to gain benefits as well as stay ahead of the curve.
Solution Highlights